Scaling up electrolyzers substantially lowers capital costs per unit due to economies of scale and manufacturing efficiencies, which shortens the payback period for green hydrogen projects. Larger systems benefit from reduced equipment and maintenance costs, especially with automated production methods. However, smaller units offer more flexibility but at higher costs and longer returns. To really understand how size influences economics and payback time, explore how renewables, technology, and project design interplay in large-scale hydrogen production.
Key Takeaways
- Larger electrolyzer units benefit from economies of scale, reducing capital costs and shortening payback periods.
- High renewable capacity factors and stable operation improve hydrogen production rates, accelerating payback.
- Modular, automated manufacturing lowers per-unit costs, enabling quicker returns on investment for scaled-up systems.
- Variability in renewable energy sources can extend payback periods unless mitigated by grid integration or hybrid systems.
- Advanced electrolyzer technologies with higher efficiencies and longer lifespans further shorten hydrogen production payback times.
Overview of Electrolyzer Technologies and Their Characteristics
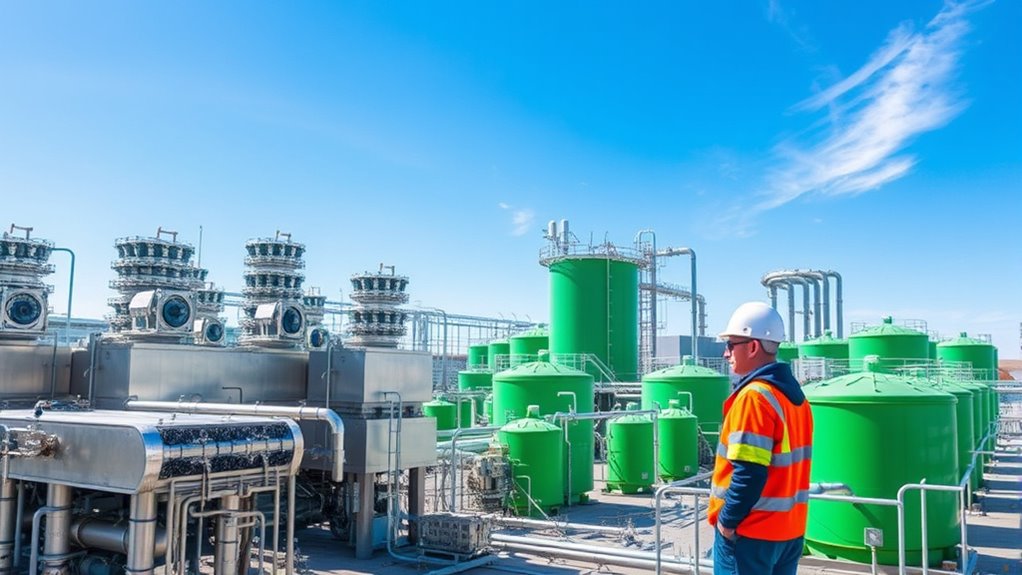
Electrolyzer technologies vary markedly in their design, operation, and efficiency, making it important to understand their distinct characteristics. Solid Oxide Electrolyzers (SOECs) operate at high temperatures with a ceramic electrolyte, achieving higher efficiency by consuming about 37.5 kWh per kilogram of hydrogen—much less than PEM or Alkaline types, which use 52–54 kWh. PEM electrolyzers use a polymer membrane, respond quickly, and are ideal for integrating variable renewable energy. Alkaline electrolyzers, the most mature technology, rely on liquid alkaline solutions but are less efficient. Emerging Anion Exchange Membrane (AEM) electrolyzers aim to combine benefits of PEM and alkaline types, targeting better durability and efficiency. These technologies vary in scale, from small distributed units to large centralized plants, each suited for different applications. The solid oxide technology’s high-temperature operation enables it to achieve greater efficiency and lower electricity consumption. Additionally, advancements in electrolyzer scalability are expanding their application range from small-scale hydrogen production to large industrial facilities.
Capital and Operational Cost Dynamics at Different Scales
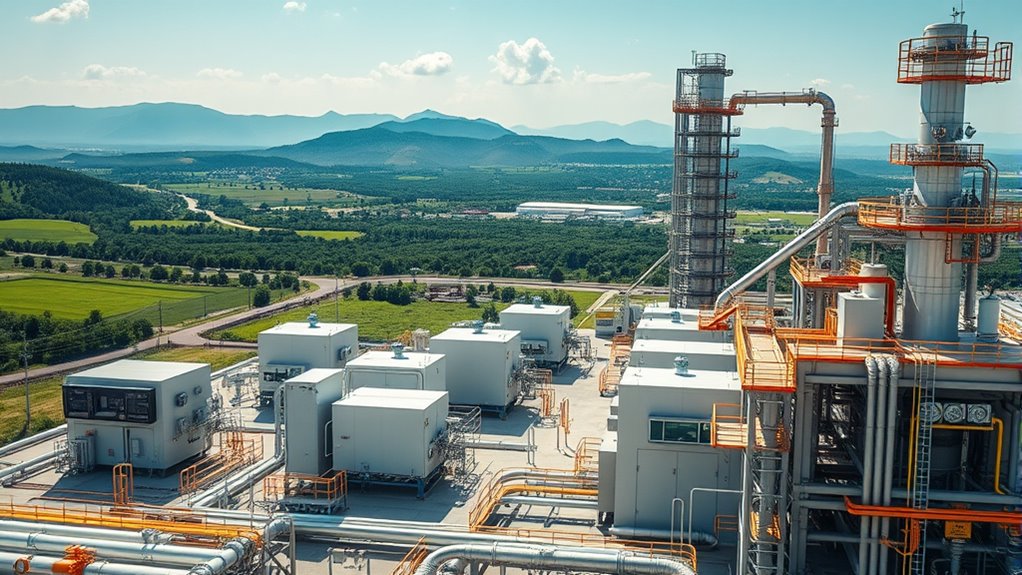
As you scale up electrolyzers, you can benefit from economies of scale that lower overall capital costs through equipment and BOP savings. However, cost variability factors like maintenance expenses and component replacements influence operational costs differently at each size. Understanding these dynamics helps you optimize both upfront investments and ongoing expenses for more economical hydrogen production. Larger electrolyzer units often face higher maintenance requirements due to increased component complexity, which can offset some savings gained from scale. Additionally, offensive security measures such as thorough monitoring and risk assessments become increasingly important to maintain system integrity at larger scales.
Economies of Scale
Scaling up hydrogen production capacity leads to significant reductions in both capital and operational costs, making large-scale electrolyzer plants more cost-effective. As capacity increases, you benefit from economies of scale, lowering per-unit capital costs, especially in materials and manufacturing. For example, the seven-tenth rule shows doubling capacity raises costs by only 62%. Larger plants also improve utilization rates, cutting operational expenses per kilogram of hydrogen. Components like power electronics and balance of plant systems scale more efficiently, further reducing costs. Manufacturing volumes grow, enabling bulk purchasing and technological advances that lower stack and system costs. This synergy of savings accelerates progress toward cost targets like $1/kg hydrogen by 2030. Additionally, cost efficiency is enhanced as improved calibration and component scaling lead to more accurate and reliable electrolyzer performance, further driving down costs.
Cost Variability Factors
Cost variability in hydrogen production arises from multiple factors that influence both capital and operational expenses across different scales. For capital costs, electrolyzer types matter: PEM units cost $1,300–$1,700 per kW, while alkaline electrolyzers are projected to decline from $1,163 in 2020 to $634 in 2050, with wide variability depending on technology maturity and scale. Solid oxide electrolyzers are still uncertain but promising. Operational costs depend on efficiency gains, such as the rise of alkaline electrolyzers from 70% to 80%, and reductions in input power, like SOEC’s 25% savings. Additionally, the use of precious metals, project size, financing costs, and technological advancements all drive cost differences, making scale a key factor in managing overall hydrogen production expenses. As the market for AI-driven optimization expands, smart system integration can further enhance operational efficiencies and cost savings.
Maintenance Expenses
Maintenance expenses for electrolyzers depend heavily on their size and operational conditions. Larger systems benefit from economies of scale, lowering BOP costs and reducing per-unit expenses. However, maintenance costs still hinge on factors like capacity factor, utilization, and stack degradation. Higher utilization accelerates stack wear, increasing replacement frequency and operational costs. Key considerations include:
- Stack replacements occur roughly every 3.5 to 11.5 years, representing about 11% of initial costs per cycle
- Longer stack lifetimes in PEM and alkaline types reduce maintenance frequency compared to SOEC and AEM
- Operating factors such as temperature, pressure, and impurities influence degradation and costs
- Larger systems may lower per-unit operational expenses through improved system efficiencies, but stack replacement remains a significant variable cost
Operational efficiency improvements can also help mitigate some maintenance expenses by reducing overall stress on components and extending lifespan. Additionally, degradation rates are affected by operational practices, which can influence overall maintenance schedules and costs.
How Scale Affects Payback Periods in Hydrogen Production
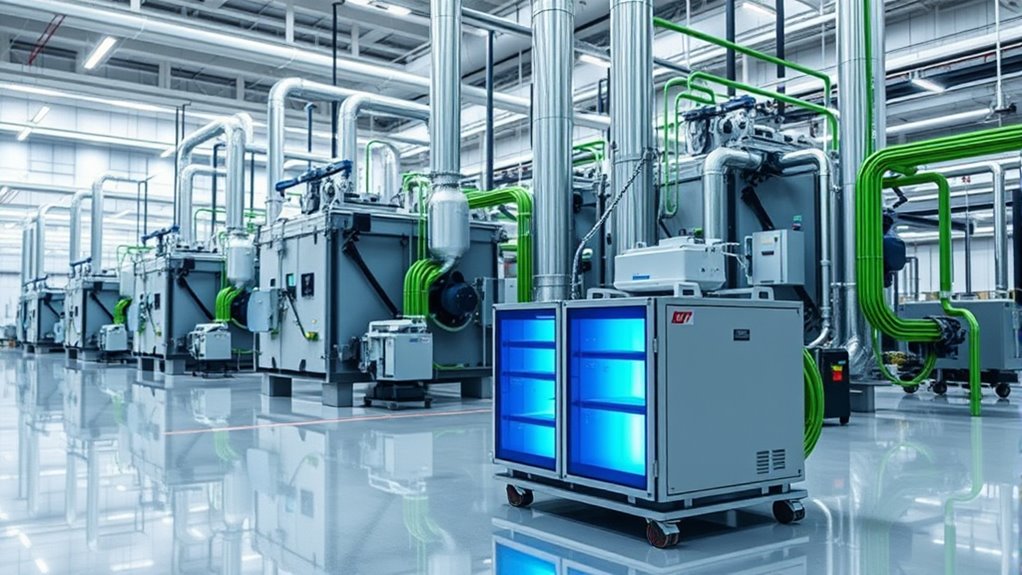
Increasing the scale of hydrogen production considerably shortens payback periods by lowering capital costs and boosting efficiency. Larger electrolyzer projects benefit from economies of scale, reducing unit CAPEX and per-kg hydrogen costs. For instance, producing 1,000 units annually can notably decrease manufacturing costs compared to smaller setups. Current electrolyzer CAPEX typically ranges from $1,000–$1,200 per kW, but large-scale deployments aim for under $200/kW by 2030, further improving economics. Higher utilization rates increase hydrogen output, accelerating project payback. Although large projects require substantial initial investment, they offer better risk-sharing, market access, and potential for rapid cost reductions through manufacturing innovations. Additionally, manufacturing efficiencies gained at larger scales can significantly contribute to reducing costs. Ultimately, scaling up shortens payback periods by making green hydrogen more financially attractive and competitive. Scaling electrolyzer capacity can lead to significant reductions in overall project costs, making green hydrogen more viable for widespread adoption.
Influence of Renewable Energy Sources and Capacity Factors
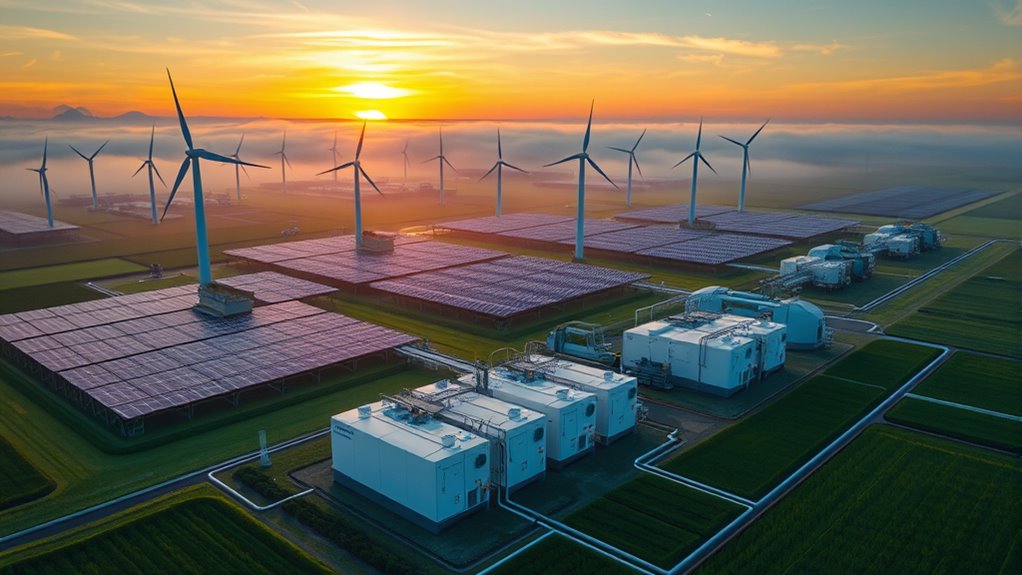
Your hydrogen production‘s success depends heavily on the renewable energy sources available and their capacity factors. Variability in wind, solar, and hydro power affects how consistently electrolyzers can operate, influencing costs and payback time. Combining different renewable sources or integrating with the grid can help stabilize supply and improve overall efficiency. Additionally, regions with higher capacity factors for renewables tend to achieve faster payback periods for electrolyzer investments. Implementing energy storage solutions can further mitigate intermittency issues and enhance operational stability.
Renewable Variability Impacts
Renewable energy sources such as solar and wind exhibit significant variability in their capacity factors, which directly impacts green hydrogen production. This variability affects how consistently your electrolyzers can operate, influencing project economics. Lower capacity factors mean less steady power, extending payback periods, especially for larger systems that need stable, high-capacity input. The fluctuations stem from factors like weather, seasonal changes, and geographic location. For instance:
- Solar capacity factors vary regionally, from 9% to 35%, due to resource profiles.
- Wind and solar output fluctuate daily and seasonally, impacting hydrogen yield.
- Weather conditions like cloud cover and temperature cause real-time output variations.
- System factors such as shading, degradation, and design choices further influence capacity stability.
- Renewable variability can also lead to increased costs for backup power or energy storage solutions, complicating project planning.
- Understanding capacity factors is crucial for accurate project forecasting and optimizing electrolyzer operation.
These factors challenge maintaining continuous hydrogen production, impacting efficiency and project viability.
Hybrid Systems Benefits
How do hybrid systems enhance green hydrogen production? By combining multiple renewable sources like solar and wind, you boost overall efficiency and reliability. Solar preheats water, improving electrolyzer thermal performance, while wind provides steady power, increasing production rates. Excess energy from these sources is utilized effectively, reducing waste. Additionally, hybrid systems improve capacity factors, leading to higher utilization and operational flexibility. Integrating energy sources with storage options further enhances system dependability. The variability of renewable sources makes hybrid systems essential for continuous operation. This approach also aligns with Prophetic Dreams concepts of harmony and balance, emphasizing the importance of integrating diverse elements for optimal results. The table below illustrates key benefits:
Benefit | Description | Impact |
---|---|---|
Increased Electricity | Combining sources raises input for electrolyzers | Higher hydrogen output |
Thermal Efficiency | Solar preheating and wind integration improve heat | Better efficiency |
Cost Optimization | Renewable mix reduces hydrogen cost | Competitive pricing |
Scalability & Flexibility | Adaptable to different sources and demands | Broader application potential |
Grid Versus Dedicated Sources
The choice between grid-connected and dedicated renewable energy sources substantially influences electrolyzer capacity factors and overall hydrogen production efficiency. Grid-connected systems can adapt operation to match renewable availability, boosting capacity factors to 77–86% and reducing costs. In contrast, dedicated off-grid setups often need extensive storage and oversizing, raising capital costs and lowering capacity factors. Benefits of grid integration include:
- Flexibility to capitalize on VRE variability
- Reduced reliance on costly storage
- Ability to sell excess electricity
- Improved system economics through avoided fuel costs
High capacity factors are vital for cost-effective hydrogen production, with hybrid renewables offering better performance than single sources. Additionally, cookie management plays a role in collecting analytics that can help optimize system operations. Ultimately, grid-connected electrolyzers maximize utilization, lower costs, and enable more efficient green hydrogen generation.
Challenges and Innovations in Industrial-Scale Deployment

Scaling green hydrogen production to industrial levels faces significant hurdles, from high capital costs and infrastructure needs to technological maturity. Currently, costs range from $3 to $6 per kilogram, much higher than gray hydrogen’s $2/kg. High capital expenditures, driven by bespoke project designs, inflate the Levelized Cost of Hydrogen and hinder competitiveness. Infrastructure upgrades are essential for transporting and storing green hydrogen, requiring substantial investments. Intermittent renewable energy sources pose challenges for continuous supply, while existing systems for gray hydrogen need repurposing for green variants. Innovations like modular electrolyzers aim to reduce costs and deployment times. Additionally, technological maturity varies across electrolyzer types, and policies or carbon pricing are critical to making green hydrogen economically viable at scale. Cost reductions in renewable energy continue to improve the economic outlook, making green hydrogen more competitive in the future.
Efficiency Metrics and Their Impact on Economics
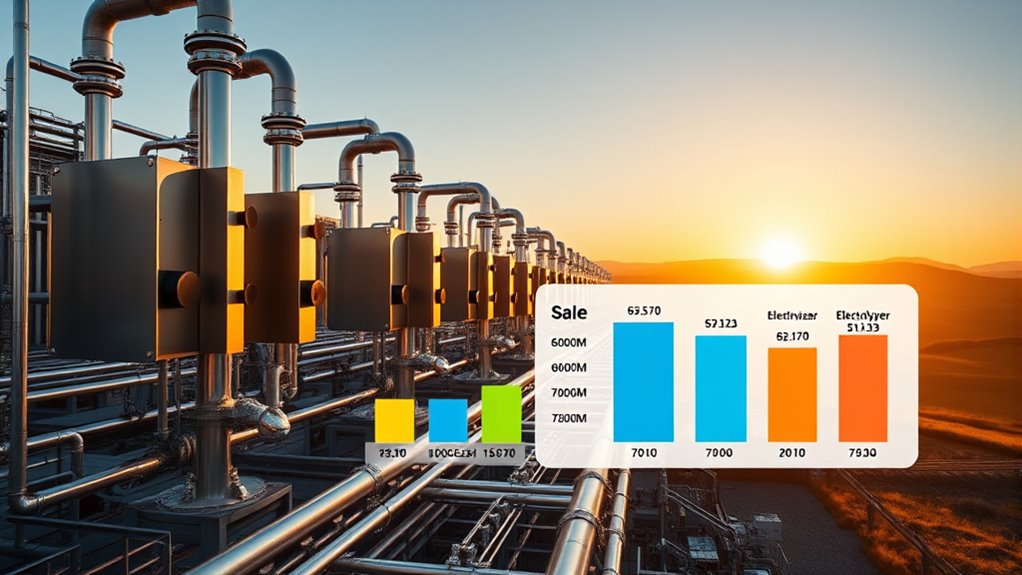
Energy efficiency metrics play a crucial role in determining the economic viability of green hydrogen production. You need to understand that efficiency is often measured as electricity used per kilogram of hydrogen (kWh/kg H2), with state-of-the-art electrolyzers averaging around 61%. Improving conditions like temperature and pressure can boost efficiency by up to 17%, but higher production rates may require more energy, reducing overall efficiency. Keep in mind, efficiency alone can be misleading; it doesn’t always reflect true performance. Monitoring overpotential helps assess durability, while standardized testing ensures fair comparisons. Accurate benchmarking is essential for industry-wide improvements.
- Higher temperatures and pressures enhance efficiency but may increase costs.
- Increased hydrogen production can decrease energy efficiency.
- Stability over time is essential for long-term economics.
- Standardized metrics ensure accurate performance evaluation.
Suitability of Different Electrolyzer Types for Various Scales
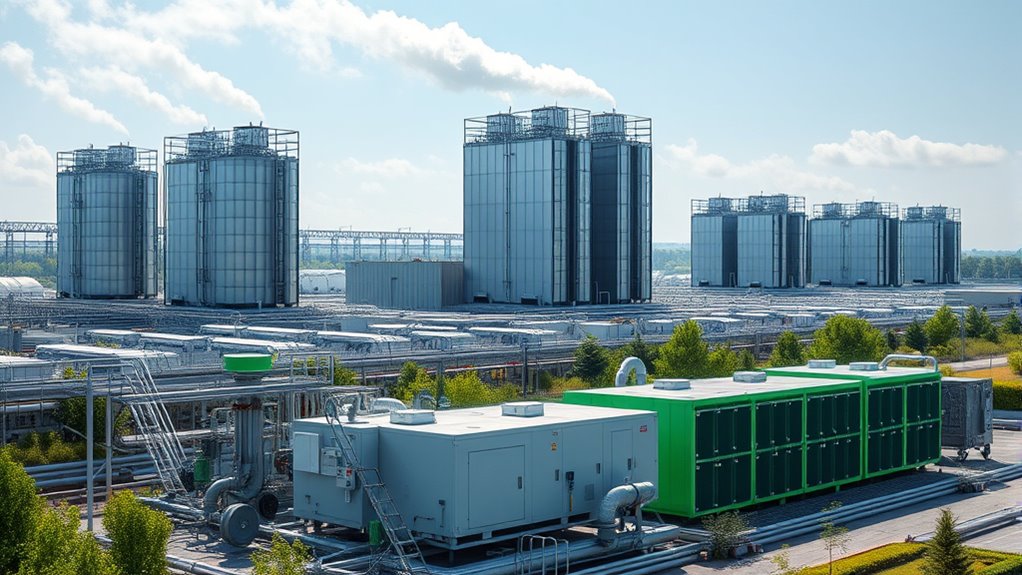
Choosing the right electrolyzer type depends on the scale of your hydrogen production needs. If you’re aiming for small to medium projects, PEM electrolysers are ideal because of their high efficiency, fast response, and compact, modular design. They work well with variable renewable energy sources, making them suitable for decentralized production. However, their higher capital and maintenance costs limit their use at very large scales. For large-scale, centralized production, alkaline electrolysers are more cost-effective and durable, offering proven performance in industrial settings like refineries and ammonia plants. They require less maintenance and have lower capital costs but are less flexible with fluctuating power inputs. Solid Oxide Electrolyzers suit large-scale industrial applications, especially where waste heat is available, though they’re still emerging technology.
Strategies for Enhancing Cost-Effectiveness at Large Scale
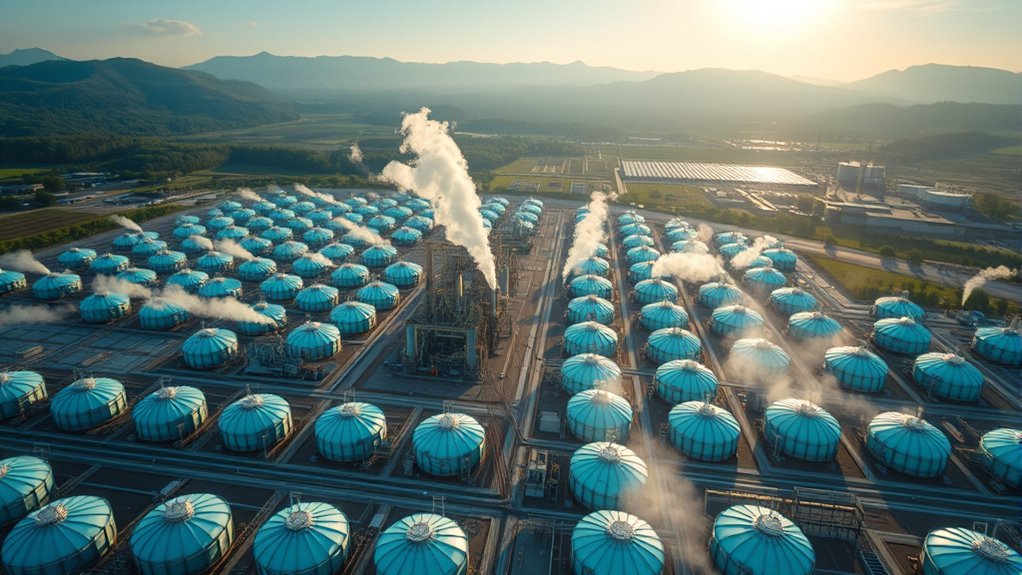
To enhance cost-effectiveness at large scale, manufacturers focus on adopting advanced manufacturing techniques and component standardization. Scaling production from 1 MW to 20 MW electrolyzer plants cuts costs by over 33%, thanks to improved performance. Automated GW-scale stack manufacturing reduces stack costs from about 45% to 30% of total expenses through mass production. Reaching 1,000 PEM electrolyzer units annually enables roughly 50% stack cost reductions, driven by better design and material efficiency. Larger plants spread fixed costs over higher outputs, lowering per-kilogram costs. Implementing continuous process improvements also significantly boosts manufacturing efficiency and cost savings.
Scaling up electrolyzer production reduces costs by over a third through improved performance and standardized manufacturing.
- Using automated assembly lines and advanced welding speeds up production and cuts labor costs
- Standardized, modular components reduce system and installation expenses
- Lowering precious metal catalyst loadings decreases material costs without sacrificing performance
- System design standardization creates economies in balance-of-plant equipment procurement
Future Outlook for Green Hydrogen Economics
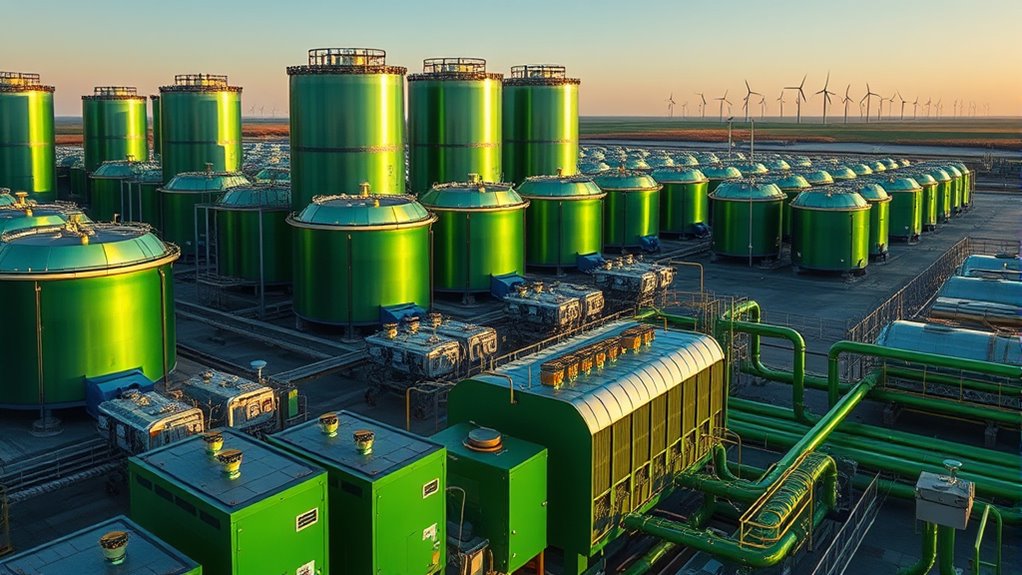
The future of green hydrogen economics looks promising, driven by rapid market expansion and technological progress. Expect the global market to grow at a CAGR of 22% to 38.5% between 2025 and 2030, reaching USD 60.56 billion. By 2050, green hydrogen could supply nearly a quarter of global energy needs. Governments worldwide are supporting this shift with policies, incentives, and ambitious goals like India’s 5 million metric tons target and the EU’s Green Deal. Technological advancements are lowering electrolyzer costs and boosting efficiency, making green hydrogen more viable. Increasing demand across industries such as steel, ammonia, and transportation fuels fuels investments in infrastructure. Market size projected to reach USD 4.59 billion by 2030 As these trends continue, green hydrogen’s role in a sustainable energy future will only strengthen.
Frequently Asked Questions
How Does Electrolyzer Lifespan Affect Overall Project Economics?
Electrolyzer lifespan directly impacts your project’s economics. A longer lifespan means you recover your capital costs more quickly, lowering the levelized cost of hydrogen and improving profitability. It also reduces operational expenses since replacements and maintenance are less frequent. With durable electrolyzers, you can secure better financing, extend system reliability, and enhance your project’s overall sustainability, making your investment more attractive and financially viable over time.
What Are the Safety Considerations for Large-Scale Hydrogen Production?
Think of large-scale hydrogen production like building a skyscraper; safety must be woven into every layer. You need continuous monitoring, proper ventilation, and expert-designed facilities to prevent fires or explosions. Address hazards like leaks and storage risks with rigorous protocols. Just as a skyscraper’s stability depends on sound engineering, your plant’s safety depends on thorough hazard assessments and multidisciplinary collaboration to keep operations secure and reliable.
How Do Transportation and Storage Costs Influence Hydrogen Economics?
Transportation and storage costs play a vital role in hydrogen economics. You’ll find that delivery expenses vary based on transport mode and distance, often making up a significant part of the total cost. Efficient storage solutions can cut costs, especially at refueling stations. Larger-scale production reduces per-unit costs through economies of scale, while proximity to renewable resources also helps lower transportation expenses, improving overall hydrogen competitiveness.
Can Emerging Electrolyzer Technologies Reduce Overall System Costs?
Emerging electrolyzer technologies can markedly cut system costs by improving efficiency, reducing capital expenses, and enabling larger-scale manufacturing. You’ll benefit from advanced designs like SOECs and AEMs, which offer higher efficiencies and lower materials costs as production scales up. Larger, modular units also decrease costs through economies of scale and automation. Overall, these innovations make green hydrogen production more affordable, supporting broader adoption and cleaner energy systems.
What Policies Most Effectively Support Large-Scale Green Hydrogen Deployment?
Think of policies as the wind propelling a ship forward. To most effectively support large-scale green hydrogen deployment, focus on robust financial incentives like grants and tax credits that lower upfront costs. Streamline regulations for quicker project approvals, invest in infrastructure, and foster international cooperation for export markets. Combining these strategies creates a strong current that carries your green hydrogen ambitions from vision to reality efficiently and at scale.
Conclusion
As you explore green hydrogen, remember that larger electrolyzer scales can reduce costs by up to 50%, markedly shortening payback periods. For instance, industrial-scale setups often see payback in just 5-7 years, compared to 10 or more for smaller systems. This shows how scaling up not only boosts efficiency but also accelerates your return on investment, making green hydrogen a more viable and sustainable energy solution for the future.
I’m Theodore, and I love tiny houses. In fact, I’m the author of Tiny House 43, a book about tiny houses that are also tree houses. I think they’re magical places where imaginations can run wild and adventures are just waiting to happen.
While tree houses are often associated with childhood, they can be the perfect adult retreat. They offer a cozy space to relax and unwind, surrounded by nature. And since they’re typically built on stilts or raised platforms, they offer stunning views that traditional homes simply can’t match.
If you’re looking for a unique and romantic getaway, a tree house tiny house might just be the perfect option.